Sailing World: Changes in Racing Sails and Sailmaking
Posted on May 9th, 2021
North's 3DL technology may lead the grand prix market, but other sailmakers have worked hard to developed their own laminate-sail technology. An in-depth look at the state of the art of sailmaking from our May 2004 issue.
May 3, 2004
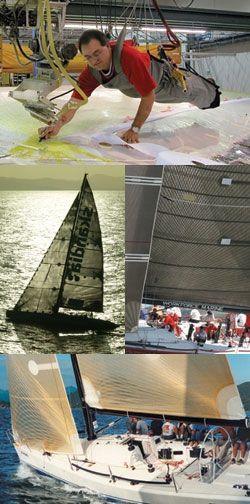
SailTech Medley
(clockwise From Top) John Burnham, Courtesy Quantum, Courtesy UK, Carlo Borlenghi/Rolex
Racing sails made of laminated materials have been the choice of leading-edge racers for nearly a quarter century. These sails, assembled from panels built of high-strength fibers sandwiched within plastic film, have continued to evolve, and the recent trend has been to design the sail first, then make each section of laminate, or the entire sail, with the expected loads of the sail in mind. In this area, North Sails' 3DL process is the clear market leader among bigger boats. For many sailmakers, existing patents have slowed development of customized lamination for these newer "membrane" sails (sometimes called "load-path" or "string" sails); but with the nine-year Sobstad vs. North lawsuit settled (in 2001) and relevant patents due to expire soon, there's been a spate of manufacturing news. Last winter the industry's biggest supplier of sailcloth and laminates, Dimension-Polyant, bought the Fraser-Doyle production facility in Australia where Doyle D4 sails are made. D-P has cloth-weaving factories in Germany and production laminators in the United States, but the D4 process gives them the capability of making extra-wide sections of laminate, produced to any designer's custom specifications. "To maintain our level in the market," says D-P USA's president, John Gluek, "it became apparent that membrane technology was a direction we had to take." D-P can now deliver custom sections, assembled, to any sailmakers' specs, including Doyle's. "It's another way for us to provide cloth," says Gluek. "The sailmaker will send in his designs, and have the selection of the yarn layout or type of fiber he wants." Gluek expects D-P will add production facilities elsewhere in the world within a couple years. Several other sailmakers are developing their own processes of making membrane sails more directly from raw materials. More than a year ago, UK Sailmakers, makers of the distinctive Tape Drive sails, began selling Ultra, a new kind of sail based on similar principles. More recently, Ullman Sails International and the Quantum Sail Design Group have announced new, unique approaches based on offshore manufacturing. And North Sails hasn't been idle, continuing to invest heavily in quality control and R&D to refine production at its 3DL plant in Minden, Nev., and expand 3DL production of smaller sails with rotary-molding machines. Before D-P's acquisition, any D4 sails in this country had Doyle logos. Sailmaker Bob Fraser, of Australia, developed the process during the '90s and made a deal with Robbie Doyle, who wanted to start selling a membrane-type sail. Doyle started slowly, with a sail on his own boat in 1999, but quickly saw the value in the sails. "Every fiber is put there for a reason and goes right to the load source; then you distribute that fiber into the sail exactly where you want," he says. "Fibers are employed much more efficiently compared to paneled sails." D-P's Gluek says the benefit is in the flexibility of working in wide sections and being able to vary fiber amounts to disperse loads more effectively. Essentially, flat sections are laid with computer-designed and -laid arrays of fibers and then laminated under heavy pressure (over 70 psi). "The advantage is light weight," says Doyle. More pressure means less glue, he says, and a lighter laminate. D-P is producing D4 under license to Elvstrom/Sobstad, which holds patents filed in the '80s by Peter Conrad at Sobstad Corp. Conrad's own membrane-style Genesis sails have gained fresh momentum since Sobstad and Elvstrom merged two years ago. Genesis sails now have seams and yarns lined up with the loads the designers anticipate. "There's no struggle," Conrad says. "The panel junctures in the sails-the seams-are perfectly lined up with the load forces. No yarn crosses any panel in the sail. If you want to build a three-dimensional context to the sail, you do it by altering the panel junctures." With production in China, there are now two types of Genesis racing sails: Lightwave, the grand-prix version, for lighter breezes; and Platinum, constructed the same way, but with an inner layer of taffeta for strength and durability with only a slight weight and thickness gain. Genesis sails use either Pentex yarn, at the low end, or Vectran, which Conrad believes is better than carbon because it's impervious to damage from flexing and creeping. Another earlier developer of membrane sails is UK Sailmakers; its Tape Drive sails are made of film with horizontal, shaped panels, reinforced by high-strength tapes. These sails have been through several evolutions over the last 17 years since UK bought Horizon Sails in 1987 and took on the technology. Both Tape Drive and Ultra, UK's new product, are pure examples of load-path construction, with separate materials used to provide the sail's structure and its surface. The development of Ultra, which meant shifting from tapes to using fibers, laid in similar patterns, was easy in theory, but a challenge in practice. Butch Ulmer, UK International's president, says, "The old adage that this venture would take twice as long and cost twice as much certainly proved to be the case, but we continue to improve the product and the process." Ultra sails begin with rectangular film sections, tacked together and laid flat on a vacuum table. Fibers pre-impregnated with adhesive are then laid from corner to corner on the film by a giant computer-controlled X/Y plotter. "We've designed the yarn layout and yarn content," says Ulmer. "We lay down 12 yarns at a time with some heat so it sets off the adhesive, and then put down a scrim on top." That's followed by film with the adhesive side down and a vacuum-bag lamination. Ulmer describes drawing the broadseamcurves on the sail, then cutting it into sections and reassembling it as a shaped sail using an ultrasonic machine and expensive glue. "The ultrasonic kicks the glue and doesn't deform the Mylar," he says. Completed skins are sent to lofts for finishing.UK continues to sell both Tape Drive and Ultra sails, and both are licensed under patents first owned by Sobstad, now by North under the lawsuit settlement terms. Nearly ready for prime time are Ullman Sailmakers' membrane sails, which will be built in China and are as yet unnamed. They're basic "string sails," says Dave Ullman, made with carbon fibers, and shaped traditionally with transverse panels. " Fibers are laid on panels at a laminator to Ullman design specs- "Commercially it's the only way to do it," says Ullman. "Laying it out as one and then cutting them like UK [Ultra] does takes forever." As described by Ullman, first a section of pre-preg Mylar is laid out and then carbon thread is laid down. The carbon thread isn't pre-preg, he emphasizes: "Pre-preg carbon gets too brittle and you can't fold it, because the carbon breaks. When carbon is soft and laid on, it won't break. Then it becomes the most durable of all the products." Ullman's sails are being built under an arrangement with the Genesis patent holder Elvstrom/Sobstad. While others focus on load paths in their membrane sails, Quantum Sail Design Group is taking a different tack with its Fusion M "Smart Sail" Technology. Larry Leonard, Quantum's president, says flatly, "They're not load-path sails." Tested on J/29s and a Farr 52, the sails have a computer-designed yarn layout based on the assumption that loads are multi-directional and that load paths change with trim and windspeed. The sails have more fiber content than most load-path sails, Leonard says, and provide significant advantages relative to North's 3DL. The sails have fibers where you would expect-up the leech, for example-but most of the tack fibers radiate out to the leech and many fibers from the clew radiate to points along the luff. Rather than running concentrically, fibers cross frequently, creating an interlocking structural grid that Leonard says handles shifting loads more smoothly. Smart Sails are laid out in a new facility in Malaysia, with arrays of fibers on standard 54- or 60-inch Mylar panels, which are pre-impregnated with adhesive. Dry aramid, carbon, or other fibers are laid down on the sticky Mylar, with tension, by a computer-controlled plotter in groups, up to 12 at a time; these panels are then laminated individually at high pressure, trimmed for traditional broad-seaming, and then assembled as horizontal panels with Quantum's seam adhesive. Because of the quality of laminate, says Leonard, the sails are produced at a competitive weight, with more shape-holding fiber than competitors' sails, or can be lighter with similar fiber content. North began 3DL production in 1992, building full-sized sails out of raw materials on adjustable molds to a designed shape. Tom Whidden, president of the North Marine Group, acknowledges improvements in technology made by competitors, but believes the 3DL process remains superior and distinct: "There are still only two technologies-making paneled sails, shaped with broad-seaming, and making a sail that's molded, which is 3DL." Whidden emphasizes the smoothness of 3DL sails, which conform to the mold's shape as the sails are laminated at relatively high heat. After the sail is built on a mold, Whidden says, 3DL's Mylar sections are there for only two purposes-to keep the wind from blowing through the shape created, and to keep the load-bearing fibers aligned with the paths of the loads determined by the designer. North's rivals say that the edges of the Mylar panels are cut on a curve to match the shape of the mold, making the sails no different from others except that they're laminated atop a three-dimensional work bench, i.e. the mold. It's true that North's panels are cut on a curve to lie smoothly on top of the mold. After being cut, the pieces are butted against each other and taped with a wide swath of cellophane-type tape before load-bearing fibers and a tear-preventing scrim (also pre-shaped) are laid down. But then, subjected to the amount of heat you might cook a meal at, the Mylar layers visibly smooth out against the mold (see photo above). "The thermoforming brittles the Mylar a little bit,"says North VP of manufacturing, John Welch, "but within its working range. It also forms the Mylar around the fibers to eliminate voids." North has 12 years of development into its expensive bet that this process creates a superior sail, and continues to refine its design and production. During the last America's Cup, North blind-tested 27 types of carbon for use in sails. It has recently rebuilt nine of its 11 molds to create a smoother, more accurate and durable mold surface. And each shipment of adhesive or other raw material is tested and samples preserved for analysis if a laminate problem occurs in that batch of sails. In another move made not long ago to improve laminate durability, North switched from using faster infrared heating to a slower conductive heating of its laminates. But the full-sized molds have their limitations. Currently, the facility operates three shifts, 24/7. For smaller sails, a new rotary molding machine promises greater speed and efficiency. The drum of that machine, introduced in Toronto two years ago, changes shape so that the Mylar film and high-strength fibers fed onto it are laminated in a three-dimensional shape. When the raw materials come off the other side of the drum they comprise the entire membrane of a laminated sail. The first machine, now retired, could make sails with a foot length of up to 13 feet. The new RM12 machine is 40 feet wide and should be operational by summer. The million-dollar question is how bullet-proof it can be. If one part malfunctions, production stops. North's competitors believe their new processes will provide lighter, faster sails at similar or lower prices. They believe that building on molds limits the quality and durability of North's lamination, and makes it stiffer and often heavier. North counters that only their sails are built exactly to their three-dimensional shape and that they're the smoothest shapes because there are no junctions caused by seams between flat panels. One thing most sailmakers agree on is that membrane sails continue to improve to the benefit of racers and, with protective taffetas applied, even cruisers. Most sailmakers also now think that a mix of carbon and aramid fibers is superior to and lasts longer than aramid alone. Dacron will remain a common choice, but laminates are now making their way in some applications into classes such as J/105s, Melges 24s, and J/24s. Sailmakers who previously might've discouraged laminate sails on smaller PHRF boats now not only report performance advantages but confidence that the newer sails can provide good value. One top sailmaker that hasn't taken the plunge yet is Halsey Lidgard; sometime next year they plan to begin selling a product they call "thread-align technology" on a limited basis. Andy Halsey says their product will be laminated and have seams, but will be shaped by more than just broadseaming. "We're a little more cautious about getting to market," he says. "There are still patent issues and people who have rushed them; it's not long until the patents disappear. Our timing will coincide with that." Several sailmakers, including Halsey, also continue making sails of that mystery material, Cuben Fiber. Developed for Bill Koch's America3 campaign in 1992 by Heiner Meldner, a nuclear weapons physicist, and R.J. Downs, an aerospace composite engineer, Cuben Fiber is the pricey choice of hot racers and mega-multihulls such as Cheyenne and Geronimo. Downs, the company president, says they do the opposite of what everybody else does. Echoing Quantum's Leonard, Downs argues against the idea of load-path sails. He says load paths "change continuously as you trim" and when you reef the sail. The Cuben Fiber process takes fibers and reduces them, says Downs, to "monofilaments in multi-layered films, each a thousandth of an inch thick. We turn it into a very thin, uniformly distributed tape. We layer those tapes, each with all its fibers oriented in one direction, and put them in different orientations." Lamination then takes place under pressure in an autoclave. Limited production capacity and high prices have prevented widespread use of Cuben Fiber, but Downs says the price is now only $13 per yard-still $4/yard higher than anything else-but cheap enough to be showing up on top 40- and 50-footers. Manufacturing of sails is changing-and seems to do so weekly. We agree, as Peter Conrad says, that it's disappointing sailmakers haven't found the ability in centralized manufacturing to offer significantly lower prices. But if, as most sailmakers indicate, newer-style membrane sails truly offer weight and shape-holding improvements, with multi-season durability, those of you on the fence may find yourself soon making the leap.